超级CSP结构与封装工艺探讨
时间:08-12-25 点击:
一、超级CSP结构与封装工艺过程
图1示出了超级CSP的封装的照片,该封装具有48个焊球,焊球间距为0.75mm,体尺寸为6.8mm×6.9mm,最大高度为1.0mm,图2示出了该封装的断面图和层结构。在制作超级CSP封装中涉及到的工艺过程如图3所示。晶圆片上的周边焊盘在光平板印刷电镀后,真正的阵列图案要重新安置。接着,在晶圆上制作大约100μm高的金属端子。采用新的密封方法把整个晶圆表面密封后,使用晶圆级封装技术制作与芯片同样尺寸的封装,此方法涉及到通过标准的划片工艺把晶圆分为单个的半导体封装。
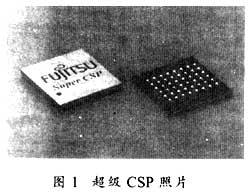
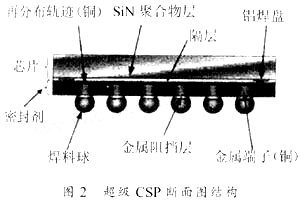
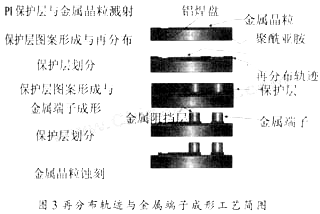
1、再分布轨迹与金属端子成形
端子成形和焊盘重新配置的第一步,就是在器件晶圆上聚酰亚胺涂层膜的成形。此涂层是防止模塑压力和应力缓冲区,这也提高了晶圆与密封剂间的黏附特性。
下一步,使用溅射把薄金属安装到晶圆表面上,此膜是由黏附金属层和导电层(通常为铜)构成,这些薄金属膜是改线工艺和金属端子成型工艺中采用的电镀基体。在薄型金属膜表面上形成图案阻挡层。通过电解镀制作再分布轨迹。完成这些工艺后,再形成阻挡层,并利用电解镀形成端子,把溅射膜进行蚀刻并完成后成形工艺。
2、 密封晶圆片
把模塑模分为两部分,上薄和下膜。如图4所示,下模有内外模组成,把这些模塑模加热到近似于175℃,并通过真空板临时膜紧贴到上模。把其上形成端子的晶圆片置于下模的内模上,并把密封剂压板放在有金属端子晶圆片的中心部位,临时膜具有3种功能,即:
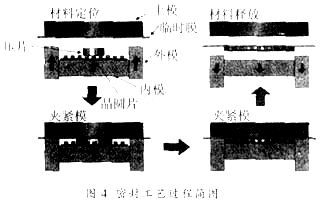
防止密封剂与上模接触,把模塑压力分配到整个晶圆片的表面上;在下一阶段使所有端子顶部露出。
当夹紧模塑模时,通过提供热和压力使密封剂压力熔化。密封剂分布于整个晶圆片表面,并通过向内拉紧模塑模而硬化,即使密封剂脱离脱模剂并具有极高的黏附力,能容易地使密封的晶圆片脱模,这是因为只有模塑模的周边部分与密封剂接触,这样就得到了有临时膜的密封晶圆片。
3、剥去临时膜
在此工艺中把临时膜从密封的晶圆片上剥去。偶尔,密封工艺阶段在端子的顶部与临时膜间的界面处,存在密封剂薄膜,焊球装配工艺后,采用规则的划片技术把密封的晶圆片分离。使用这些工艺过程。制造出与保护的芯片一样大小的超级CSP产品。
二、超级CSP封装密封剂及密封工艺
通常,密封剂是由具有优良的塑流特性的联二苯环氧树脂组成,这样的密封剂在1989年作为制造4MbitDRAM而引入,自此,随着高密度填充物添加技术的先进性,人们研发了含有大约90%质量的硅填充物,具有高度可填充和塑流性材料,含有大约90%质量的硅填充物密封剂的CTE接近于硅的状况,这使得在此密封剂中使用弹性体、柔性增强剂是不必要的。直到对此有要求。因此,由于使用的有机元素绝对量的减少,密封剂易燃性较低,那么,抗易燃性元素的采用显得不必要,而在过去是必要的,BGA超级模塑面阵列封装(SMAAP)的出现,能够使制造者改进密封工艺方法,采用超级模塑阵列封装,消除了使用脱模剂,这在传递模塑技术中绝对需要的,这些新的密封材料因此具有比较早期材料更简单的成分,同时,为芯片提供更好的保护,超级CSP的解决方法遵从同样的途径,涉及简单的生产方法和生产结构,在别的封装中使用的很多成分,在超级CSP材料中是不需要的。例如,超级CSP不使用插件。这表明它比使用插件的传统封装要求工作阶段较少,并形成较少的边界。表明较低的生产成本和出现有缺陷产品的可能性较少。超级CSP还具有别的优点,虽然用户能够采用传统的表面安装技术装配超级CSP,但是作为面阵列封装,超级CSP不要求下填充树脂。超级CSP产生于2个关键技术工艺的研发,其一,晶圆片上表面密封工艺技术,包括金属端子,把这些金属端子的顶部裸露,进行彻底密封。其二,是合适的密封剂研发。
根据封装尺寸,传统的模塑封装需要不同的模塑模,要求制造商制作与封装尺寸一样多的模塑模。这使传统的模塑技术没有通常使用的液态密封技术方便,然而,超级CSP克服了这一缺陷,采用超级CSP技术,密封剂覆盖整个晶圆面积,应用于φ150、φ200、φ300mm的标准晶圆尺寸,因此超级CSP的用户不需要准确很多不同类型的模塑模。像由超级CSP使用的模塑成形密封剂是一种优良的密封工艺,原因在于几个方面,例如,模塑成型密封剂法提供的在高温和高压的状况,各种材料的塑流及硬化法,这意味着模塑成形密封法允许使用具有极高黏度的密封剂,包括在室温状况为固态的各种材料。
表1示出了采用液态树脂和传递模塑方法的滴涂法密封的DIP42 I/O管脚,间距1.27mm封装的可靠性试验结果范例,用于评定的液态树脂由a、b、c3个公司提供。如表1所示,通过传递模塑方法密封的密封式芯片特别坚固且可靠,相比较,在室温和标准压力状况下,滴涂方法使用流动的各种材料,其形成了没有传递模塑方法密封式坚固的封装形式。再者,在传递模塑方法中,硬化现象发生于高压状况之下,迫使密封剂与聚酰亚胺接触。在芯片和密封剂间,形成良好的界面。在新的密封技术工艺研发的早期,已探讨了使用传统传递模塑工艺技术的可能性,没有发现厚度小于100μm,大于φ200mm的填充空腔空间的合适的密封剂,在密封剂上设法安装20 000个端子,密封剂的厚度为100μm或比要求有增强型黏附性的密封剂更薄。
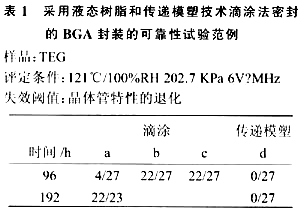
这意味着从用于传递模塑的高可靠密封剂中释放出脱模剂,超级CSP密封工艺方法,基本上由传递模塑过程和压缩模塑过程构成,显现为解决这些问题能够形成一层既薄又可靠的密封剂。
三、密封结构对可靠性的影响
评定了该封装,并对装配可靠性进行了试验,采用球栅阵列封装(45个焊球,间距为0.75mm)履行该封装评定。设计两种焊盘栅阵列封装的试验。表2示出了用于评定封装的技术参数,封装体尺寸为4.5mm×9.00mm,单个封装元件通过温度循环、压力锅蒸煮试验、高温暴光试验和表3所示的湿敏性试验,再者,有关板级可靠性试验,安装在板上的封装通过温度循环试验、压力锅蒸煮试验,弯曲试验和自由落体试验,提供的可靠性如表4所示,尽管凸点支座的典型数值极低,还是不得不注意到没有失效现象发生。
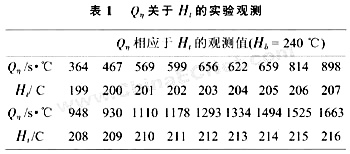
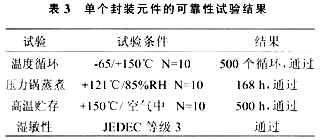
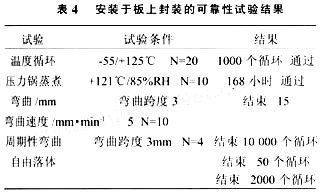
以上表明了焊接互连的热疲劳寿命与凸点支座的平方成正比,至少与考虑塑料变形有关,把有同样技术规范(I/O数45,间距0.75mm,到中点距离=3.23mm)的芯片直接安装到木板上而不需要下填充树脂。若凸点支座高度不超过400μm,在第一次失效时循环数不大于1000个,即使适度的T/C试验条件为-40℃-125℃。
为什么超级CSP的板级可靠性试验结果是良好的,而不考虑极低的凹点支座高度?原因可能是:
(1)超级CSP封装密封剂的CTE接近于母板的CTE,因而该密封层有效地降低了在焊料互连部分发生的应力。
(2)具有高黏附强度的密封剂增强并固定芯片和端子精密的互连部分,并且也不允许其变形。
(3)焊球和端子的连接部分具有坚固的结构并能够承受应力,因为焊球占有整个金属端子的表面,从密封剂突起并拥有堆形结构。
通常,插件起着放松由于芯片和母板不匹配产生应力的重要作用,图5示出了IC封装端面图结构的照片,在此封装中IC芯片通过直接粘接技术与插件形成互连。插件是由FR-4基板芯构成的有机基板,并构成了作为表面层。插件的CTE几乎与母板一样,因为芯体的主要成分是由玻璃纤维编织而成且具有低CTE的环氧树脂的玻璃布的化合物。IC封装装配方法的特点是把先前准备的插件通过DCA方法与芯片互连。图6示出了超级CSP分成两组的断面图。有助于人们理解,上部分示出了有电极的正规芯片,下部分示出了"插件"。通过金属端子通路把在密封剂上形成的改线轨迹与焊球进行电连接,图7示出了超级CSP断面图结构的照片,在密封剂部分可观察到精细硅填充物,通过调整填充物含量,人们可以确定密封剂的CTE,从而灵活地降低在焊料互连部分出现的应力,硅填充物具有插件中存在的玻璃纤维同样的功能(=CTE匹配)。
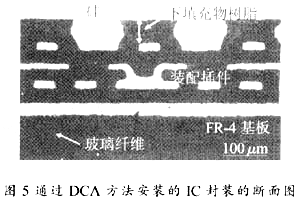
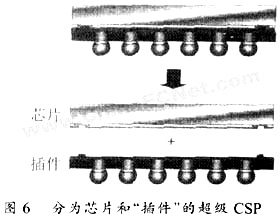
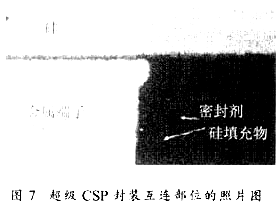
金属端子的顶部具有像弯曲表面一样的堆形结构,并从密封剂表面突出。完成超级CSP的密封技术工艺。
金属端子的顶部表面贴上临时膜,这具有足够的柔性和厚度,结果,通过剥去临时膜,移去顶部表面附近的密封剂。脱模后,把临时膜从密封式晶圆片上剥掉,具有堆状结构的表面暴露出来,并且从密封剂突出,把焊球紧紧地连接到端子的整个顶部,如图8(a)所示,可推断出,这样的互连结构比如图8(a)所示的把平面焊盘连接到焊球的BGA普遍结构更牢固,相信超级CSP对具有大的DNP和细终端间距及多I/O管脚的器件而言,肯定是有效的选择,这类器件没有凸点支座充足的高度和焊料的连接的面积。
